IIoT Cloud Platform
Googoltech’s IIoT cloud platform is a highly customizable information platform based on the core operation and control products of Fixed High and integrated with information technology, which can adapt to the interconnection of industrial equipment network, provide value-added services for customers, create a new ecosystem of technical services, and open up the last kilometer of industrial applications.
The platform communicates with the cloud platform through the network communication function of the controller. It can be used quickly without too much development through the device control, sensor layer, scheduling layer and information management layer.
Focus on equipment and data
● Always design the platform from the point of view of the device to make it more suitable for the application scenario of the Industrial Internet of Things, not just focusing on data transmission
Powerful performance
● Adopt on-demand response mechanism and adapt to large-scale device access.
● Instrumentable data acquisition and analysis
● Remote fault diagnosis, real-time monitoring and early warning
● Online debugging and function modification
● Introduction of 3D model, online simulation
Simple and easy to use
● Software is easy to use, and it takes only three steps for the user to start analyzing the data and visualizing them.
Let users operate
● Platform gives users maximum freedom to build further use of equipment data, turning boring site management of equipment into innovative Remote Monitoring
Building user communities
● Users can not only build their own applications, but also share their own applications with other users and bring benefits.
Converter Station Fault Diagnosis and Maintenance
Project Background
The converter station is the foundation of the DC transmission project, and the converter valve is the core equipment of the converter station. If the cooling equipment fails and cannot be effectively cooled, it will cause power interruption, affect the economy and people's livelihood, and bring huge losses to society. Therefore, ensuring the "zero failure" operation of the equipment has become the core requirement of the converter station.
Project Solution
At present, the converter station needs to achieve the goal of "no emergency shutdown event". Therefore, taking the converter valve cooling system as the research object, through improving the equipment basic information database, setting the vibration and related process monitoring points, the monitoring and diagnosis methods for the equipment status of the cooling system are studied, and the monitoring and diagnosis technical rules for the converter valve cooling system of UHVDC transmission system are realized. The fault diagnosis analyzes the vibration data and frequency spectrum, predicts the possible location of the fault, and generates the maintenance work order; the real-time data of PLC is automatically associated in the maintenance work order to provide more accurate basis for maintenance.
Through the optimization of monitoring means combination, as well as the improvement of platform auxiliary diagnosis and information management functions, the safe and stable operation cycle of cooling system is effectively improved, and the fault diagnosis and maintenance time is shortened. Carry out the whole life cycle management of the converter valve cooling system to provide good support for the later spare parts and maintenance service.
Solution Features
● Using edge computing system, the data is kept on the client side to protect the privacy of equipment operation data and intellectual property rights.
● Based on the requirements of converter station and management units, develop multiple systems to meet the requirements of different business parties.
● Provide equipment data monitoring, real-time early warning and evaluation of system status, intelligent fault diagnosis, preventive maintenance and scientific management of spare parts and other functional modules to realize equipment life cycle management.
Solution Architecture
Based on the monitoring point of single valve cooling system in converter station, the vibration sensor is installed on the pump to collect vibration signals from different positions to the Janus@Edge edge computing system. The controller of valve cooling system is Siemens PLC, which is connected t to Janus@Edge through an intelligent industrial gateway to collect PLC data. The intelligent industrial gateway transmits the data to Janus@Edge through the local area network, and finally Janus@Edge sends the data to Neptune@Cloud via 4G. Janus@Edge provides upper-level applications such as online monitoring and intelligent diagnosis of the converter valve cooling system in UHVDC transmission system.
Domestic Wastewater Treatment
China's problems in DWWT
● Heavy burdens on government: no charge for rural residents.
● Huge investment in sewer networks: total length has exceeded 630,000 km.
● Difficulties in operation and management: lack of monitoring, unaffordable long-term operation costs.
● Vastly distributed service points: there are over 600 thousand villages.
● Centralized wastewater treatment plants are being stretched to their limits with the emerging urban structures.
System Design and Development
Series Products ranging from 5T to 10000T
Remote Operation and Management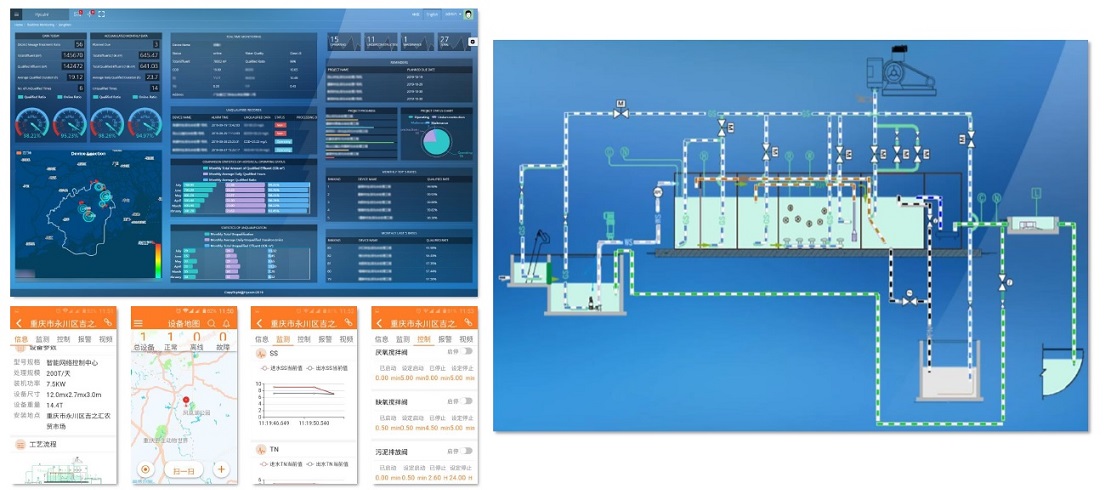
Solution Features
● Adopt edge computing technology to keep data in the client to protect data privacy.
● With the continuous accumulation of system data, the data model is continuously upgraded and more accurate.
● Can be connected to data collection and data transmission of different manufacturers and different equipment.
● The edge computing system can provide data docking capability for professional equipment operators through open platform and API.
● Edge computing systems, cloud platforms, sensors, and controllers are independently developed by Googoltech, which can provide vertical integrated solutions from sensing, control, communication, edge, and cloud information.
Solution Architecture
The secondary water supply water quality monitoring system is mainly composed of GEM intelligent controller and Janus@Edge edge computing system through industrial 4G router networking. GEM intelligent controller connects various water quality sensors, meters and HMI touch screen. The controller has a built-in Triton@Device data client, which uploads water quality, pump room operation data, and pump room video to the Janus@Edge in real time. Based on data, Janus@Edge provides upper-level applications, including water quality monitoring, pump room energy consumption monitoring, pump room equipment operation and maintenance, and water quality feature analysis based on big data models, alarm prediction, and pump room evaluation.
● Abnormalities in water quality and equipment can be predicted, alarms can be triggered, problems can be found early, risks and losses can be reduced.
● Real-time management of water quality and pump room, the upgraded from passive management to active on-demand management.
● The analysis suggestions provided by the water quality characteristic model, alarm prediction model, and pump room evaluation model are available for management decision-making.
● Remotely manage the equipment in the pump room to reduce operation and maintenance costs.
● It can be connected to the water management platform of the Water Affairs Bureau to reduce secondary development costs.
AI-Enhanced Welding System
China's problems in postindustrial era
● China is rapidly becoming an aging society.
● Facing sever labor shortage: by 2022 there will be 22 million fewer manufacturing workers.
● The welding labor market has reached 1.92 trillion RMB in 2017, but there is a gap of 3 million welders every year.
Eye in hand system
● Online vision positioning: to ensure positioning accuracy at 98.5%.
● Pre-welding defect identification and online welding process compensation based on deep learning.
● Using in-depth analysis and iterative learning of defect tags to determine repair actions after welding.
Dynamic 3D reconstruction and automatic calibration
● Dynamic 3D reconstruction helps robot quickly obtain spatial state information of workpieces.
● Auto-calibration system quickly establishes the relationship between working surface and robot’s coordinate system.
Process and trajectory planning
● Based on the characteristics of weldment to plan the welding process, parameters, trajectories, and postures.
● Rapid process trajectory verification through simulation and emulation.
● Process trajectory optimization based on online and offline analysis of real welding process data.
Hardware Configuration at Edge
The welding robot workstation is composed of welding robots and industrial cameras, and connects multiple types of equipment with the Janus@Edge edge computing system through a local area network. Through the multi-protocol access function of the Triton@Device data client and Janus@Edge edge computing system, the equipment realizes the data interconnection of various heterogeneous equipment, real-time collection of robot motion trajectory data, welding machine settings and feedback parameters, and workpiece weld pictures. It is transmitted to the edge computing system to provide welding process data management applications and intelligent decision-making in the edge computing system.
Welding Procedure
Welding Quality Analysis at Edge
Content Welding Quality Analysis in Cloud
- Datasheet - Janus@Edge 2020-07-01
- Datasheet - CNV-EC7704 2020-07-01
- Datasheet - Neptune@Cloud 2020-07-01
- Datasheet - Intelligent Manufacturing System 2020-07-09
- Datasheet - Triton@Device 2020-06-19